EMS
The Case for Early Integration of Environmental Monitoring Systems in Pharmaceutical and Biotech Facility Design
Feb 24, 2025
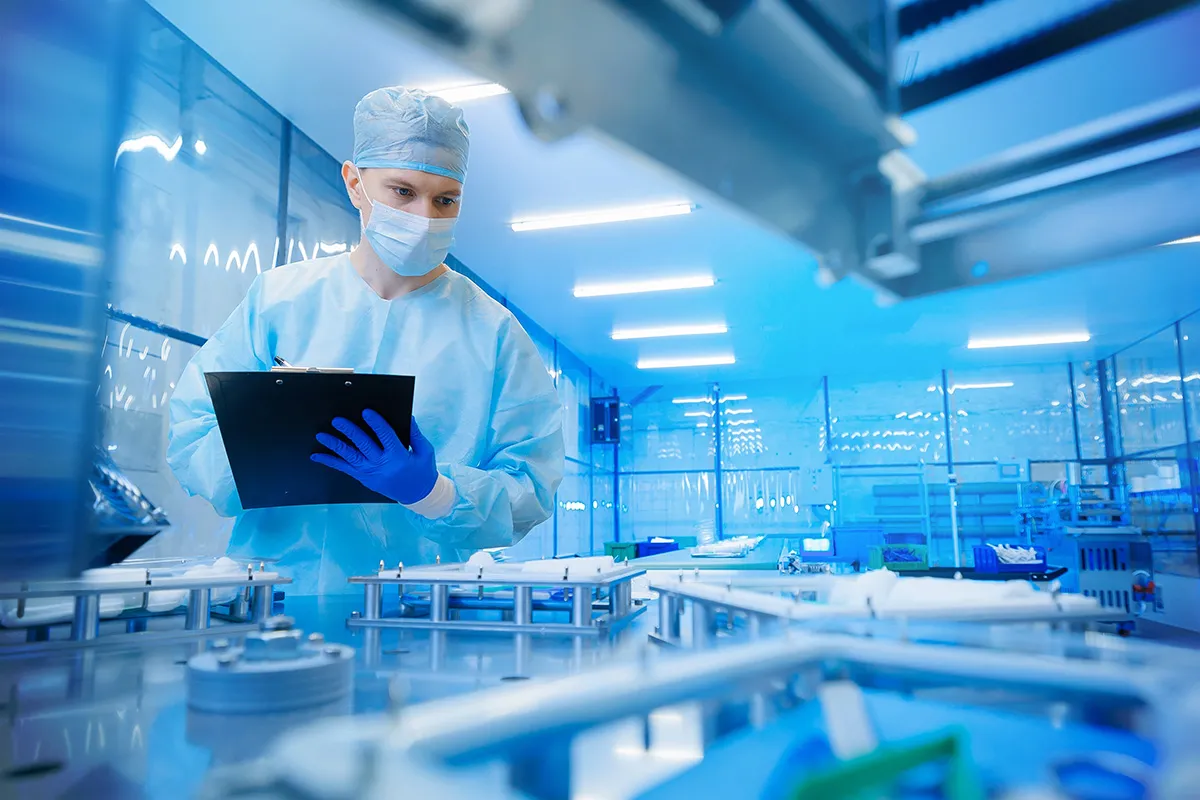
In pharmaceutical and biotech facility design, Building Management Systems (BMS) are often a top priority from the outset. These systems play a critical role in controlling HVAC, lighting, and energy efficiency, ensuring that facilities operate within optimal conditions. However, Environmental Monitoring Systems (EMS)—which track critical parameters such as temperature monitoring, humidity monitoring, and differential pressure monitoring—are frequently treated as an afterthought. This oversight can lead to significant challenges, including integration difficulties, increased costs, and compliance risks.
The Consequences of Delayed EMS Implementation
When an environmental monitoring system is not considered early in the design phase, facility owners are forced to retrofit monitoring solutions into existing infrastructures. This reactive approach creates several problems:
- Integration Challenges – A late-stage EMS implementation may not seamlessly communicate with BMS, leading to inefficiencies in facility management and requiring additional resources to bridge system gaps. A poorly integrated EMS may lack interoperability with BMS, leading to disjointed workflows, data inconsistencies, and increased complexity in facility management.
- Increased Costs – Retrofitting an EMS often involves additional hardware, software modifications, and labor-intensive installation processes, increasing overall project costs. This includes reconfiguring facility layouts, installing additional wiring, and implementing new calibration protocols to align with compliance requirements.
- Regulatory Compliance Risks – Facilities operating under FDA 21 CFR Part 11 and GMP regulations must ensure that environmental conditions are continuously monitored, recorded, and securely stored. An ad hoc EMS implementation may result in gaps in compliance, requiring costly remediation efforts to meet regulatory requirements. Additionally, delayed implementation can lead to issues such as incomplete audit trails, missing data logs, and inadequate alert systems for temperature excursions. Ensuring there are no gaps in FDA and GMP compliance is critical when designing these specialized facilities.
- Data Management Inefficiencies – A well-integrated automated temperature monitoring system allows for streamlined data collection, analysis, and reporting, which is essential for audits and quality assurance. Delayed integration can lead to siloed data and inefficiencies in quality control processes. Without early planning, facilities may struggle with inconsistent monitoring practices across different storage units, such as refrigerator temperature monitoring and freezer temperature monitoring.
- Risk to Product Integrity – Environmental fluctuations can directly impact the quality and stability of pharmaceuticals, biologics, and other temperature-sensitive products. Without an efficient EMS in place from the beginning, facilities run the risk of undetected environmental deviations, which can compromise product integrity and result in costly product losses or recalls.
ROI of Early EMS Integration vs. Adding Later
Investing in early EMS planning and design significantly reduces long-term costs and operational inefficiencies compared to retrofitting an EMS later. Based on Rees Scientific's experience, companies that integrate EMS during the initial facility design phase typically save up to 30-40% in total implementation costs compared to those that retrofit later. These cost savings come from eliminating the need for infrastructure rework, avoiding extended downtime for installations, and reducing labor costs associated with retrofitting.
Additionally, early EMS integration minimizes compliance risks, which can result in costly regulatory fines, product recalls, or delayed facility approvals. A well-planned EMS also enhances operational efficiency, reducing maintenance costs and streamlining compliance audits by ensuring all environmental data is accurately recorded from day one.
For facilities that integrate EMS after construction, costs increase due to the need for additional sensors, software upgrades, and potential facility downtime required to retrofit monitoring equipment. The indirect costs, including lost productivity and extended validation timelines, further contribute to a lower ROI when EMS is not planned from the outset.
The Case for Early EMS Planning
To avoid these pitfalls, facility designers should incorporate EMS into the earliest phases of facility planning alongside BMS. Doing so offers several key benefits:
- Seamless Integration – When EMS and BMS are designed in tandem, data-sharing capabilities can be built in from the start, reducing the need for custom workarounds. This ensures that environmental monitoring is seamlessly embedded into the overall facility control system, facilitating more accurate and comprehensive data collection.
- Regulatory Readiness – Early consideration ensures that EMS is aligned with compliance requirements, facilitating adherence to FDA, GMP, and other regulatory standards without last-minute changes. Facilities can implement standardized protocols for monitoring critical parameters, ensuring that all temperature-controlled environments are continuously validated.
- Cost Efficiency – Designing an environmental monitoring system into the facility blueprint prevents costly retrofits and minimizes disruptions to operations. A proactive approach reduces labor costs, prevents duplicate infrastructure investments, and enhances long-term sustainability.
- Optimized Operational Efficiency – A well-integrated EMS supports proactive quality control, enabling real-time temperature monitoring, refrigerator temperature monitoring, freezer temperature monitoring, and corrective actions to maintain optimal conditions. Automated alerts and reporting functions can help facility personnel respond quickly to environmental deviations, minimizing potential risks to product quality.
- Enhanced Scalability – Incorporating EMS early allows facilities to plan for future expansions, ensuring that additional equipment, storage units, or production areas can be seamlessly integrated into the monitoring infrastructure without major system overhauls.
Conclusion
As the pharmaceutical and biotech industries continue to advance, facilities must adopt a forward-thinking approach to environmental monitoring. By prioritizing EMS at the same level as BMS in the design phase, companies can ensure streamlined operations, meet regulatory requirements, and achieve long-term cost savings. Investing in early EMS integration is not just a best practice—it is a strategic decision that enhances efficiency, safeguards product integrity, and ensures seamless compliance with industry standards.
By planning ahead and integrating an environmental monitoring system from the start, pharmaceutical and biotech facilities can achieve greater reliability, regulatory adherence, and operational success, all while reducing costs and mitigating risks associated with late-stage EMS implementation.
For more information about how Rees Scientific’s EMS can be incorporated directly into your design plans, please reach out to our team.