EMS
Choosing a Temperature Probe: What Regulated Facilities Need to Know
Jul 21, 2025
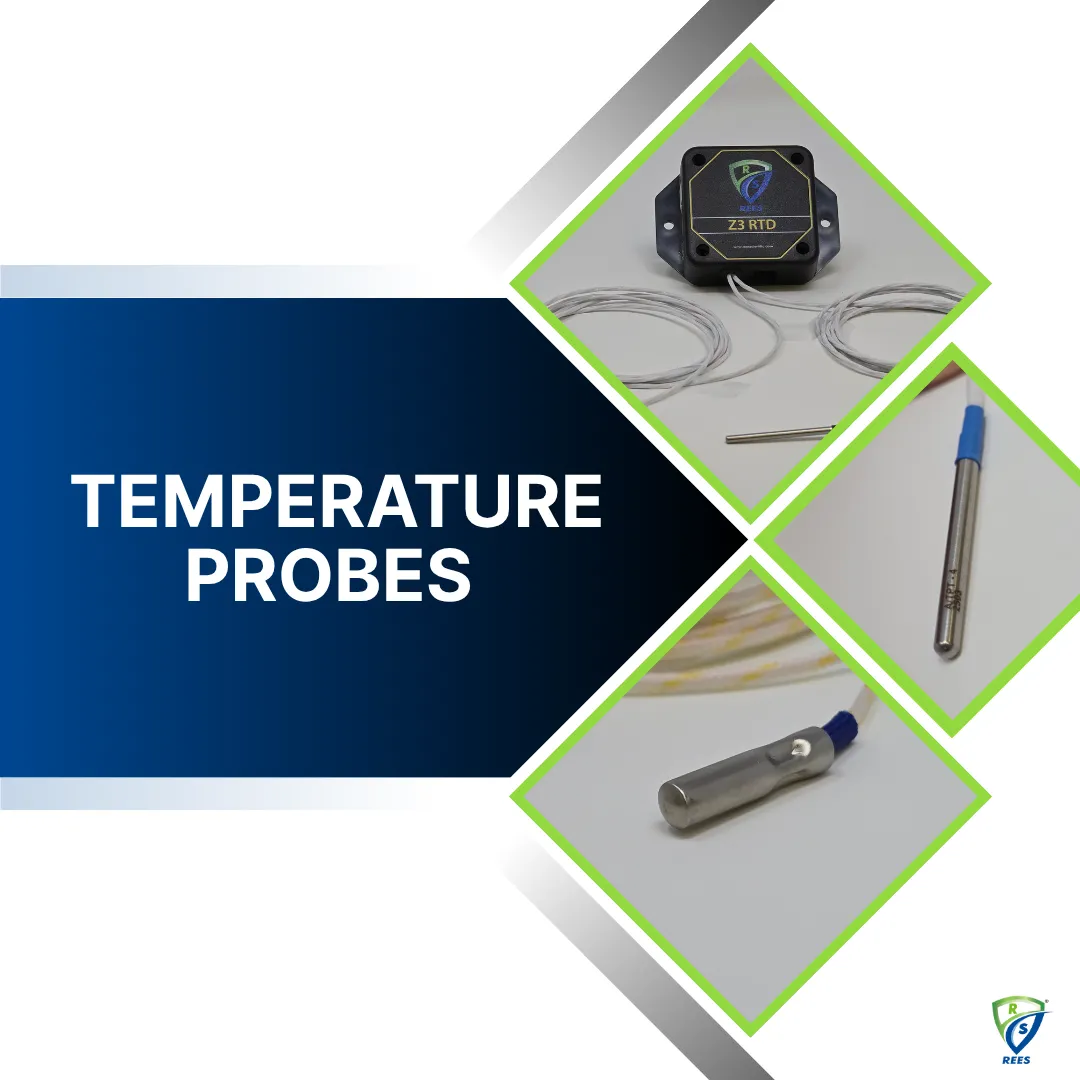
Temperature monitoring is foundational in life sciences, clinical labs, healthcare facilities, and biomanufacturing, but it's rarely as simple as placing a sensor and walking away.
Behind every well-monitored freezer, incubator, or cleanroom is a probe chosen for a specific reason. And getting that choice wrong can mean unreliable data, nuisance alarms, or worse, failed audits and compromised product.
Here’s what to know when selecting a temperature probe for regulated, high-risk, or critical environments.
1. Start with the Right Probe Type for the Job
The first step in building a reliable monitoring system is choosing the right kind of sensor. Each type has trade-offs in accuracy, range, response time, and durability, and each is better suited for specific environments. When choosing a temperature probe, understanding the trade-offs between RTDs, thermistors, and thermocouples helps ensure data in any application.
RTDs (Resistance Temperature Detectors):
- Used in: Pharmaceutical manufacturing, GLP/GMP labs, blood banks
- Why: RTDs are highly accurate (often ±0.1°C or better) and have excellent long-term stability. They’re a top choice for equipment that stores high-value, temperature-sensitive materials, like plasma, vaccines, or reference standards, where compliance depends on precise, documented control.
- Example: A -80°C ultra-low freezer used to store clinical trial samples would typically use an RTD for its stability and precision.
Thermistors:
- Used in: Hospital pharmacies, diagnostic labs, university research
- Why: Thermistors respond quickly to small temperature changes, making them useful in environments where short-term fluctuations matter, like medication storage units that are opened frequently.
- Example: A hospital refrigerator holding insulin or vaccines might use thermistors to monitor for even minor deviations that could affect efficacy.
Thermocouples:
- Used in: Industrial R&D, stability chambers, sterilization tunnels
- Why: Thermocouples are ideal for extreme temperatures (up to 1,800°C or more) and harsh conditions. While less accurate than RTDs, they’re highly durable.
- Example: In a cleanroom environment running hot-cycle equipment validation, thermocouples are used to confirm that sterilization cycles are reaching and sustaining required temps.
Choosing the wrong sensor type, say, using a fast-reacting thermistor in a stable freezer, or a slower RTD in a frequently opened fridge, can create noisy data or miss meaningful events.
2. Simulate Product Temperature and Choose the Right Buffer
In temperature monitoring, there's often a disconnect between what’s being measured and what matters. Most deviations don’t occur because a product’s core temperature suddenly shifts, they happen when systems measure air temperature too literally.
To bridge that gap, facilities often use thermal buffers to simulate how actual products, like blood, reagents, or cell therapies, absorb and release heat. The idea is to mimic the thermal inertia of stored materials, filtering out noise like door openings or fan cycles that don’t pose a real risk.
Two common buffer types are:
- Glycol bottles: These are small vials filled with glycol or similar fluid. They're easy to use and can approximate the thermal behavior of certain liquid-based products.
- Metal temperature blocks: These solid blocks, typically made from aluminum or stainless steel, have a pre-drilled cavity for the probe. Their consistent thermal mass provides a more controlled and predictable buffering effect over time.
While glycol is widely used, metal blocks offer some key advantages, especially in regulated or critical environments. Unlike glycol, metal doesn’t evaporate, leak, or degrade over time. It provides repeatable thermal performance without the need for regular fluid replacement or evaporation checks.
In applications like pharmaceutical storage, blood banking, or biologics, where data integrity and reproducibility are important, the stability of a metal temperature block often makes it the preferred choice.
The takeaway? Buffered measurement is essential, but how you buffer matters. Choosing the right thermal mass helps ensure your data reflects product safety, not just ambient conditions.
3. Look for ISO 17025 Certified Probes
When accuracy is mission-critical, calibration matters just as much as the sensor itself.
ISO/IEC 17025 certification ensures that the lab calibrating your probes follows internationally recognized methods, uses validated equipment, and maintains full traceability. It’s the standard most often requested (or required) during audits by FDA, EMA, and CAP inspectors.
- Example: A biotech startup submitting stability data to support an IND application needs temperature data tied to ISO 17025 certified sensors, because regulators want to know that every degree reported is backed by a validated calibration process.
Without this certification, it’s hard to prove that your “2–8°C” really was 2–8°C.
4. Calibrate, Document, and Re-Calibrate
Even the best sensors drift. Over time, all probes should be recalibrated, ideally on a defined schedule based on equipment use, criticality, and manufacturer guidance.
Key things to verify:
- Every probe has a unique identifier linked to a specific asset or location
- Calibration certificates include both as-found and as-left readings
- Documentation is archived and easily retrievable during audits
This isn’t just a box to check, poor calibration documentation is one of the most common pain points during inspections.
Final Thoughts
Temperature sensors are the unsung heroes of compliance and product safety. Choosing the right probe, simulating real-world conditions, and ensuring certified calibration builds a foundation of trust in your data, in your processes, and in your regulatory position.
If you're evaluating new sensors or reassessing your monitoring program, Rees Scientific offers ISO 17025 certified temperature probes, solid metal temperature blocks for buffered measurements, and full-service calibration to help meet the requirements of even the most demanding environments.
How Rees Scientific Supports Your Monitoring Strategy
At Rees Scientific, we’ve been working alongside hospitals, research institutions, pharmaceutical manufacturers, and life science organizations for decades. We understand the environments you operate in, and the pressures you face when it comes to protecting critical inventory and staying audit-ready.
That’s why our temperature monitoring solutions are built around:
- High-accuracy, ISO 17025 certified probes for compliance and confidence
- Durable metal temperature blocks that simulate product temperature for more stable and meaningful monitoring
- Application-specific sensor options, whether you're monitoring an ultra-low freezer, a room-temperature warehouse, or a cleanroom hot zone
- Full calibration support with documentation that stands up to regulatory scrutiny
We don’t just offer sensors, we help you match the right ones to your equipment, risk level, and workflow. Whether you’re outfitting a new facility or replacing outdated hardware, we’re here to guide you through the process and back you up with the service and expertise you need.
The process of choosing a temperature probe is foundational to long-term monitoring success. The right sensor, buffer, or calibration strategy helps ensure trust in every data point. To learn more about our temperature monitoring sensors, visit our product page or get in touch with our team to discuss your specific application.